G’day Folks, I have some photos and commentary on laying track on the Sidetrack modules.
The quality of some photos may be a bit below par due to being taken outside, at night, under a single light, on our front verandah, when day to day life events and temperatures allowed me to work.
The photos come from the laying of track on two 160mm wide and 250mm track length modules (248mm woodwork length). The displayed sequence is correct although the photos may alternate between the two modules. The 160mm width is to allow for some more space for either 3 tracks or industrial structures behind the rear track. The 250mm length is partly because of the single point on the 2 to 3 track transition module and because I was starting to run out of room on the table! I will play around with ideas for corner modules a bit later.
First off, PAINT the modules to seal them, both outside and inside.
Then mark out the edges of the track locations for the Kato Unitrack which has a 25mm width on its plastic ballast, and which for Sidetrack using Peco Set-Track points has a 35mm track centers.
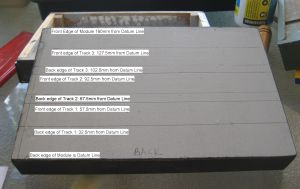
|
Marking out Track locations
|
Next mark out two lines 20mm from the ends of the modules and running parallel to the ends. Then stick down sheets of 3mm thick balsa wood between the two new lines and at the total width of the number of tracks you are going to lay. This forms a roadbed/underlay for the conventional N gauge track so that its height matches the Kato Unitrack. When glue has dried, paint!
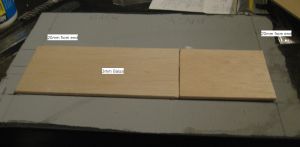
Taking your 30mm (or so) long piece of Unitrack (in this case it’s just the Unitrack base threaded on to some existing flexible track) and on the underside mark out a line 20mm from the Unijoiner end.
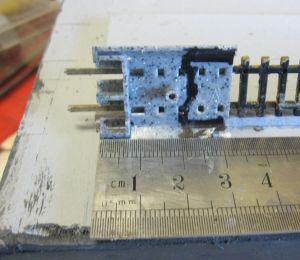
|
Marking out Unitrack end piece for trimming of Ballast slope
|
Turning the Unitrack upside down, cut through the ballast slope edges of the Unitrack until you touch the actual track base.
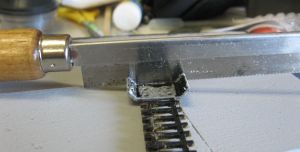
|
Cutting off ballast Slope Cut 1
|
Then from the top cut off the sloping ballast edge until you reach the transverse cut.
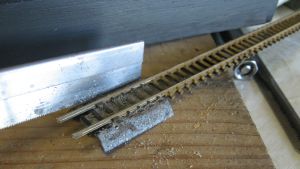 |
Cutting off ballast Slope Cut 2
|
Then break off the ballast slope.
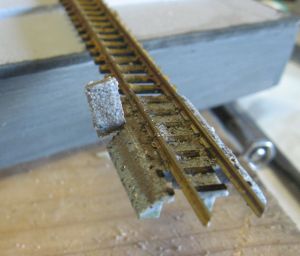
|
Cutting off ballast Slope Breaking off ballast slope
|
When you have done this for both sides drill holes for the track pins. The first hole is drilled through the hollow column under the Unitrack, This is Kato’s built in fixing point.
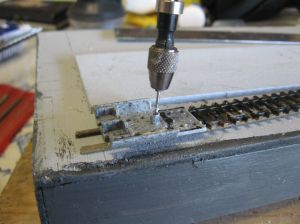
|
Drilling for track pins 1
|
Then on both sides of the track drill holes in the corner between the outside of the Unijoiner pockets and the beginning of the ballast slope.
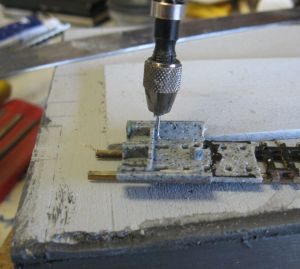
|
Drilling for track pins 2
|
Take some Silicon Wet Area Sealant, or similar, to use as a glue for the track. This wonderful stuff feels weird on the fingers, does actually hold the track down, and yet will peel or rub of when you need to get rid of it.
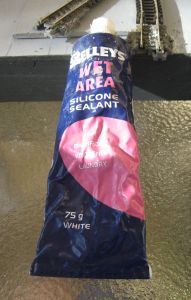
Apply three dabs of the Silicon sealant in the spots shown.Ber careful to keep the area where the Uni-joiners go clear of sealant, tricky, but necessary.
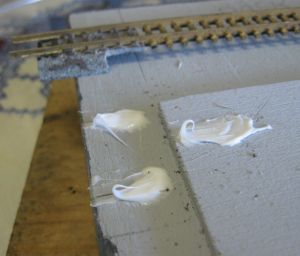
Locate the track into its position and push down into the Silicon paste. Use a 1mm thick steel ruler to allow you to work out the 1mm overhang.
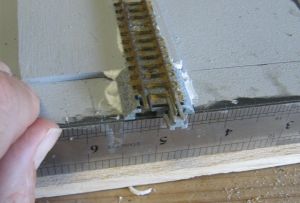
|
Fixing down Unitrack End 1
|
Carefully push a track pin in to the first drilled hole. Then follow this with pushing in two more track pins into the other two holes. Because of the wood frame these last two pins will not push all the way down. Carefully using a nail punch hammer the pins into the wood frame.
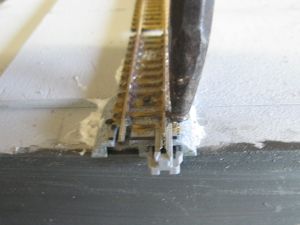
|
Fixing down Unitrack End 2 Track Pins
|
When you have let the first piece of track set in the silicon for a few hours you can locate and fix down the adjacent piece of track using a jig made out f two Peco track spacing jigs.
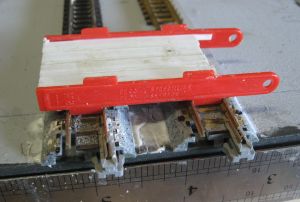
|
Fixing down Unitrack End 3 Using track spacing jig
|
Because this end of the track has some rail sticking out the end I used Xuran Track Cutter to trim it back to length.
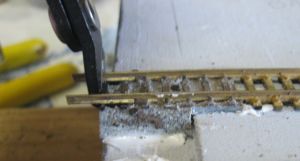
|
Fixing down Unitrack End 4 Xuron Rail cutter to trim ends
|
How the other module ended up.
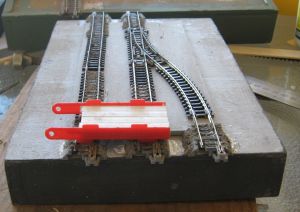
|
SideTrack 2 to 3 Track Transition 1
|
|
SideTrack 2 to 3 Track Transition 2
|
For all sorts of tips and tricks for fitting Unitrack in with conventional gauge track go to pages 19 to 21 of the Australian T-TRAK Guidelines at:
http://t-trak.nscale.org.au/guidelines